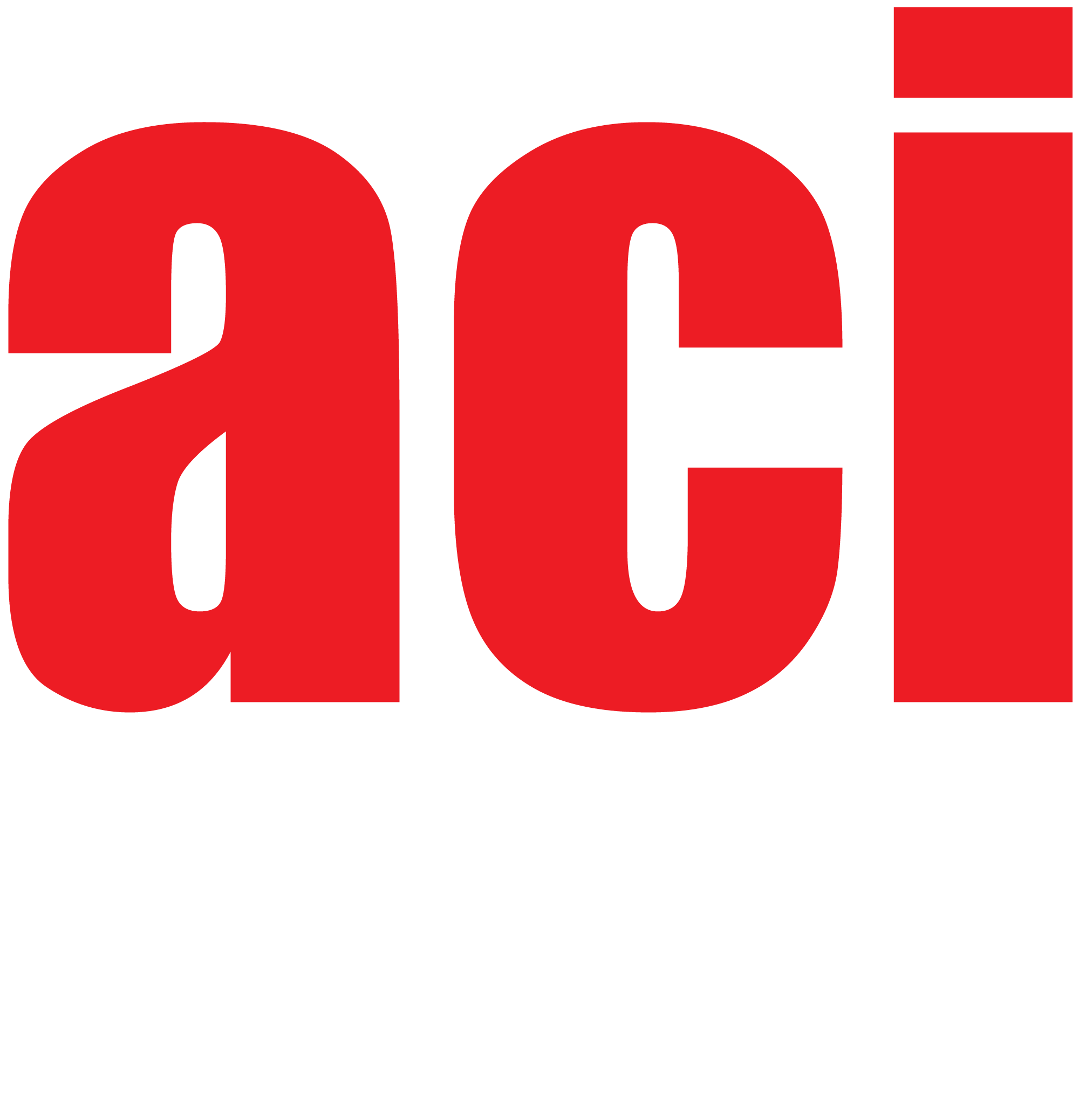
The draft wireless arm for industrial processes of high risk consist of a detailed study of anthropometric movements of a person, these parameters allow to specify the values of range, scope, and turns that must reproduce the robotic arm, the same arm is commanded by a sensory flex glove, equipped with sensors; the intercommunication and reproduction of movements such as finger, hand, elbow and shoulder are driven from the glove placed on the operator and located at a distance considered not to risk for the worker; all these movements are the result of a simulation in Matlab and reproduced by Arduino boards in their physical connection; wireless communication is done via Bluetooth to a HC05 master - slave and scope of proven range of 15 to 20m separation man - workplace. Each of the elements of the robotic arm are tested and simulated with Solidworks, ie static analysis, material selection and dimensional aspects prior to running the 3D printing piece by piece and conclude in the assembly step; along side the assembly movement mechanisms and servomotors sized for a maximum clamping force range from 18 to 22 kgf which is what a normal person has the capacity; expected outcome is to safeguard the integrity of workers in relation to elements of occupational health and safety in environments with conditions of handling of toxic substances.
viewed = 1497 times