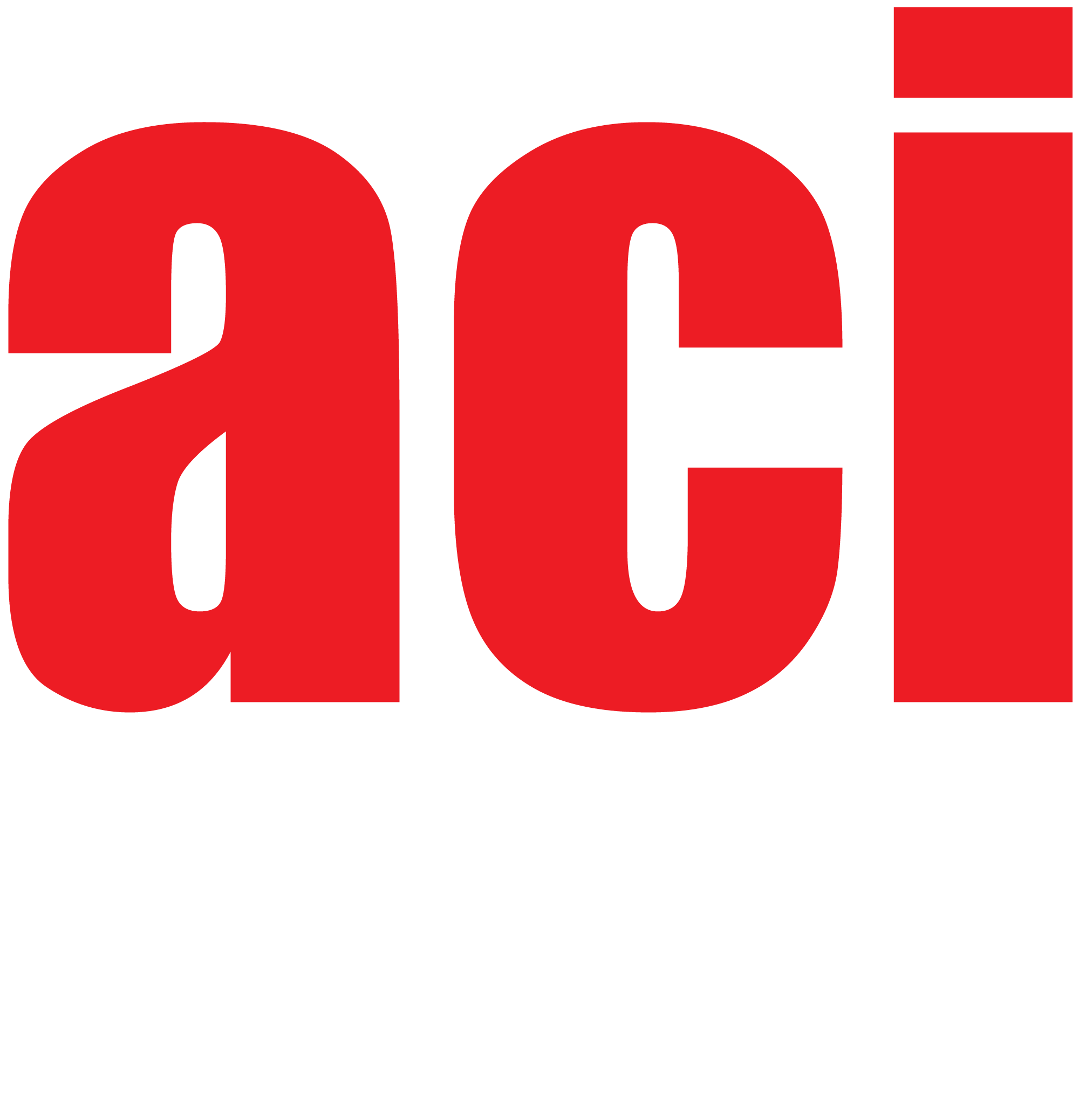
In this work hard chromium electroplating process is developed on small test specimens on AISIA36 steel. This paper includes the development of hard chrome plating process at laboratory scale and provide a simplified procedure for industrial applications. By applying a differential power over the A36 steel submerged in an electrolytic bath of chromic acid, a thin coat of 30 to 80 microns of chrome is deposited over the specimen. The hard chrome deposition is achieved by a combination of multiple variables such as: chromic acid concentration, substrate metal, anodes, current density, solution temperature and time. From the abovementioned parameters, the time and the current density are the working parameters to be manipulated while the others remain unchanged. For these experiment, a linear simplified model is theoretically and experimentally derived from Faraday’s electro-deposition law for hard chrome plating. The thickness variation, micro-hardness and cracking network of the combination of the working parameters are included and discussed in this work. The chrome deposit obtained is microscopically and gravimetrically measured. The results obtained by combining the working parameters show hardness values within the range provided of 66 to 70 HRC. This paper studies and analyzes the possible causes that influence hardness with the microstructure (number of surface cracks, density) and processing parameters such as time and current density.
viewed = 1409 times