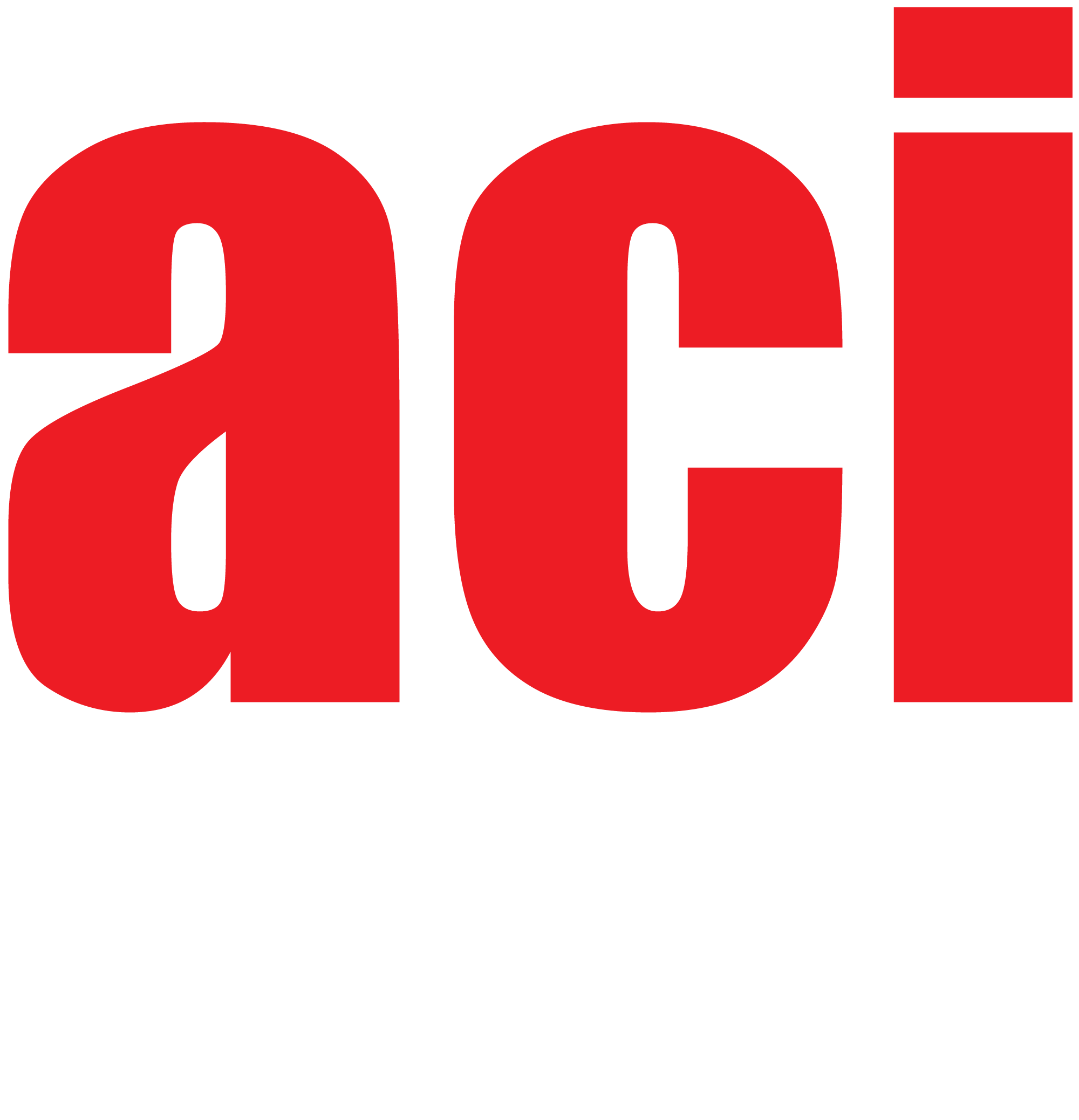
El gas licuado de petróleo (GLP) es un producto de primera necesidad, principalmente de uso doméstico, que representa el 10.4% de la demanda energética del Ecuador. A falta de mecanismos para la valorización de los residuos lignocelulósicos en el país, se planteó una ruta de conversión de biomasa a butano como sustituto del GLP, mediante un diseño computacional para evaluar su viabilidad técnica, económica y ambiental. Se seleccionó el residuo óptimo para su conversión a GLP en base a la tasa de generación anual y composición físico-química, la configuración de la ruta se diseñó en AspenPlus® con una entrada de 77 t/h de biomasa. En función de los resultados se realizó un análisis económico y de ciclo de vida usando el software openLCA®. La producción de butano alcanzó las siete toneladas por hora y una densidad energética de 26.7 MJ/L. En cuanto al eje económico, el precio de venta mínimo calculado fue de 1.03$/kg, considerando la venta de la lignina como coproducto. De esta manera, el biocombustible fue competitivo con el precio de venta al público de un dólar por kilogramo de GLP. Finalmente, la huella de carbono total del proceso fue de 102 g CO2-eq/MJ, valor superior al estándar europeo de 94 g CO2-eq/MJ. Esta investigación abre la puerta hacia la optimización de los recursos y transformación de la matriz energética del país.
viewed = 594 times